EPS Hot Melting Machine
The EPS foam hot melting machine compress foam by screw heating melting extrusion way, then make the foam scraped into an EPS foam compression blocks. After compaction, the waste Styrofoam can be reused to make other products, such as frame products and construction moldings.
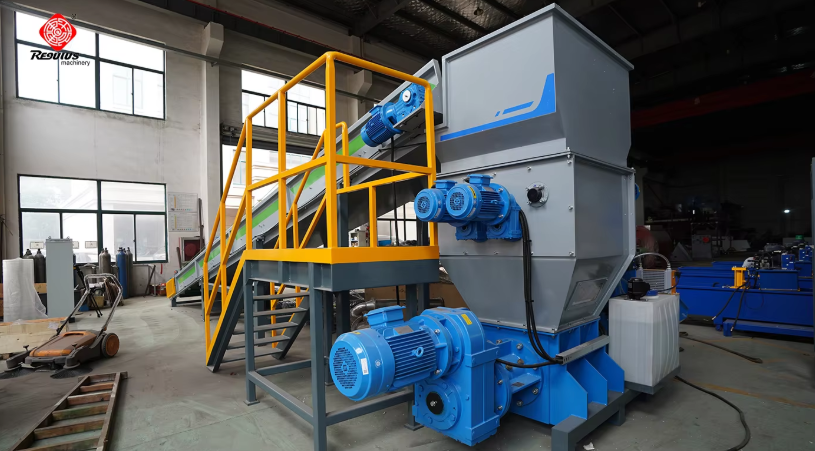
Product Application
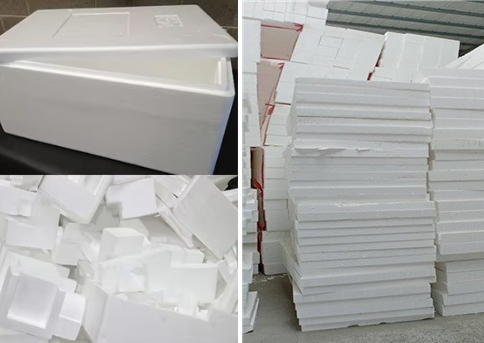
Application:
It is suitable for EPP EPE XPS PUR EVA EPS plastic foam and polystyrene foam,
such as foam box, EPS foam board, EPS foam fast food box, etc.
Our Advantages
a. Automatic cutting device
improves processing speed and adapts to mass production needs.
b. Screens, screws, blades and other accessories are made of wear-resistant materials.
Special treatment is made to resist high temperature and deformation, ensuring the stability of melting.
Reduce replacement costs
c. PLC control system
improves automation level and overall operation efficiency.
Details Images
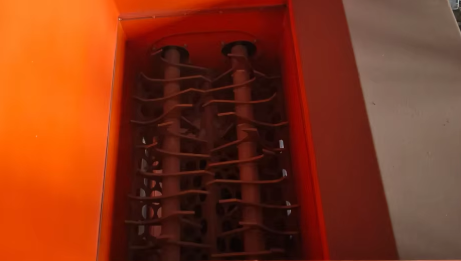
Twin Shaft Crushing Blade
High-strength material
Made of wear-resistant material, with high hardness and corrosion resistance.
Can withstand long-term, high-intensity operation.
Optimized design
It can evenly crush EPS materials and reduce material jamming and damage.
Easy maintenance
The blades are easy to replace and adjust.
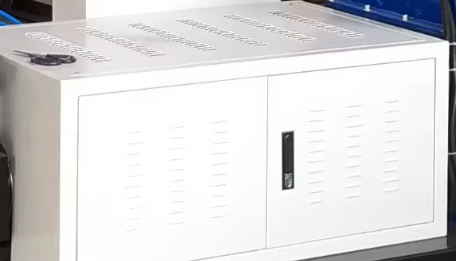
Heating Unit
High efficiency
Adopting advanced heating technology, EPS materials can be melted quickly
Precise temperature control
Ensure that the melting process is uniform without affecting the quality of the material.
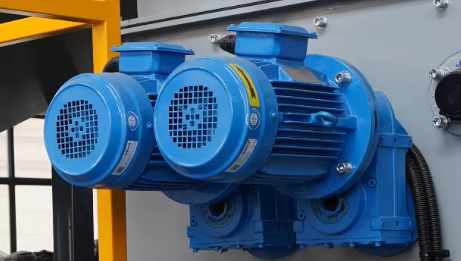
Two Crushing Motor
The use of two axis crushing knives can effectively break the plastic foam material.
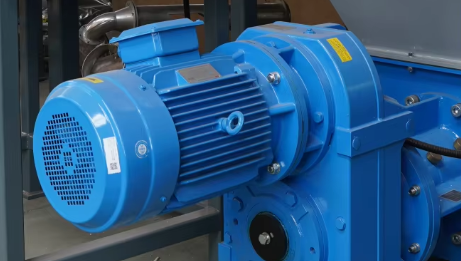
Main Motor
The motor operates efficiently and can continuously provide strong power.
Ensure the smooth operation of the hot melt machine’s crushing, extrusion
and melting functions. Siemens brand
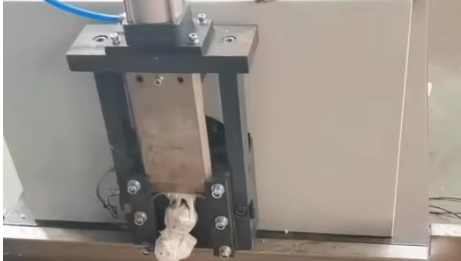
Pneumatic cutting ,automatically
Automatic cutting of finished products
After the EPS material is hot-melted and formed, the cutting device can
cut the formed material into the required size.
Ensure cutting accuracy The cutting device is controlled by PLC, with
precise positioning and neat cutting edges. This ensures the consistency of the finished product.
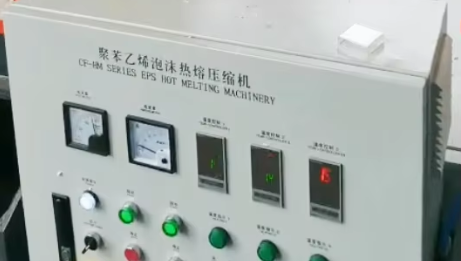
Electrical control cabinet
Equipped with complete overload, short circuit and leakage protection devices.
Use high-quality electrical components to ensure reliability in long-term operation.
Product Paramenters
Small Hot Melting Machine:
The crushing chamber is specially designed by our engineers. The blades are more efficient and the crushing chamber is larger. All blades are at special angles, this design can press the material down into the screw barrel to increase the capacity.
This machine is divided into three parts
a. Hopper
b. Crusher accessories
c. Extruder
This small machine is used in supermarkets, seafood markets, hotels. Customers buy the machine, put the machine in different places, and then customers can collect materials in different places and then sell the materials.
Feeding size |
460*400mm |
Screw diameter |
φ80mm |
Screw speed |
100r/min |
Heating power |
2.7kw |
Main Motor power |
5.5kw |
Crusher motor power |
3kw |
Crusher blades quantity |
7sets |
Machine weight |
580kg |
Medium and large hot melt machines:
The double-shaft crushing knife is used to break the polystyrene into smaller pieces and enter the screen. The crushed material is transported to the cylinder, heated by the heater to melt the material. The molten material is then transported to the circular die, where the material begins to cool down and is extruded from the die for recovery. The cutting machine automatically cuts it according to the required size to complete the production process.
Feeding size |
650*400mm |
900*600mm |
1000*900mm |
Screw diameter |
φ138 mm |
φ190-120 mm |
φ190-120 mm |
Screw speed |
165 r/min |
110 r/min |
150 r/min |
Heating power |
3kw |
10kw |
10kw |
Main Motor power |
7.5kw |
15kw |
22KW |
Crusher motor power |
3kw |
3kw*2sets |
3kw*4sets |
Crusher blades quantity |
8sets |
8+9sets |
10+11+10+11sets |
Machine weight |
900 Kg |
1500kg |
2200kg |
Previous:
PA PC PET Crystallization Dehumidification Drying Equipment
Next:
EPS Plastics Granulating Pelletizing Line